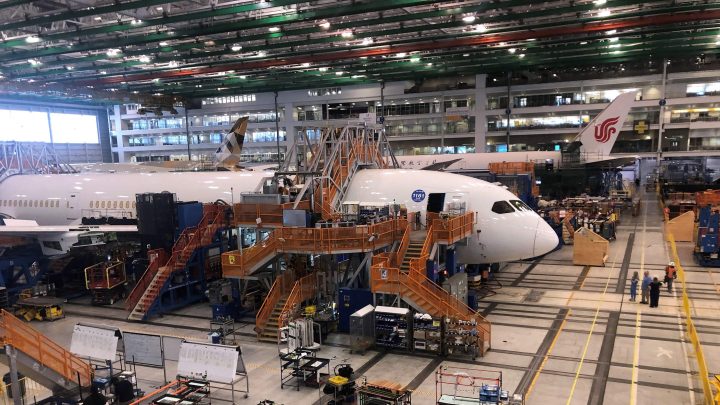
Boeing failures are a case study of America’s manufacturing “dark age”
Boeing failures are a case study of America’s manufacturing “dark age”
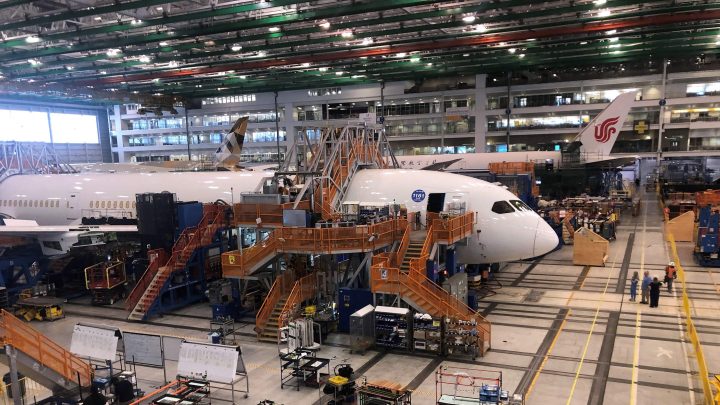
Boeing released its first-quarter financial results Wednesday, and, despite the disastrous Alaska Airlines flight earlier this year and the ensuing public scrutiny the plane manufacturer has faced, the report was not as bad as expected. Revenue came in slightly higher than forecast, but still down 8% from the year before.
Boeing has a storied history that reaches back well over a century. Its current problems raise the question of how we got here — and magnify worries about American manufacturing at large.
Jerry Useem, a contributor to The Atlantic, joined “Marketplace” host Kimberly Adams to talk about Boeing and what he calls the dark age of American manufacturing. An edited transcript of their conversation is below.
Kimberly Adams: You open your piece with a pretty stark comparison of Boeing of the past and Boeing of more recent days. Can you lay that out for me?
Jerry Useem: Well, the comparison is a stark one in that early in Boeing’s existence, it paid very close attention to the process of manufacturing. And the original founder, Bill Boeing, had his office right in the building adjacent to the shop floor and would often stroll over and inspect individual pieces. And what we’ve arrived at now is a situation where the management of Boeing is very much detached from the actual building of its planes.
Adams: Can you briefly sort of take me through the timeline of Boeing, of how they went from this superprestigious company that was doing everything in-house, had all of its engineers very plugged into what was going on, to what we’re learning as these investigations continue about such a disparate chain of events that led to, you know, the door blowing out on the plane and things like that.
Useem: The timeline is kind of a long one. I think it was in the early 2000s that a lot of the key decisions were made. And airplanes are that kind of business where the errors of yesterday take a long time to show up. But around 2005, they really got serious about what they called offloading. And this meant doing less and less of the work in-house. You know, for some of its planes, having the wings built elsewhere, having the entire tail section built elsewhere. But they took this further and further. And I’d say, prior to the accident, it was beginning to recognize that it had taken this too far and was beginning to sort of reintegrate and try to make some steps to bring itself back to kind of its engineering-manufacturing roots.
Adams: How common is what Boeing has done in the rest of American manufacturing?
Useem: I think it’s actually not uncommon. It’s a very visible case for what I think has been a fairly pervasive phenomenon. I mean, as recently as the early 2000s, Intel was seen as the absolute last word in manufacturing prowess, and its CEO frankly admitted that it lost its edge on the shop floor. And they’ve pronounced what he’s called a “death march” to get back to leadership and the actual process of making things better, ensuring quality, etc.
Adams: Yeah, one of the issues you point to in American manufacturing is that power in these companies like Boeing moved from engineers to financial managers. How did that happen, and what’s been the consequence?
Useem: The engineers who first were sort of in charge of the executive suite when the American corporation came to be. Henry Ford and Bill Boeing, these were people who arose from the shop floor. And over time, it’s been pretty well documented that the CEO class came to be populated by people out of the finance function, which meant they spoke the language of numbers and accounting, they didn’t speak the language of engineering. And so those best equipped to understand how to put things together were no longer in charge. And I think that’s a process that’s now gone too long, gone too far.
Adams: What’s the lesson for other American manufacturers to take from this situation? Not just, you know, what Boeing is doing right now, but how Boeing got to this point?
Useem: I think the lesson is ignore the process of making at your peril. You know, a lot of people have set up the Boeing story as sort of a case of a company that’s put costs in front of quality. But the thing is, really what they’ve done is actually made it more expensive for themselves. I mean, they’ve had their production lines shut down. This is extremely costly. So you’ve got to find sustainable ways to keep on driving costs down, keep on improving quality. So it’s a matter of: Are you going to do it bluntly, by getting rid of your experienced workers, your advanced machine tools, and the managerial attention required to make those continual improvements? Or are you going to lean into it?
There’s a lot happening in the world. Through it all, Marketplace is here for you.
You rely on Marketplace to break down the world’s events and tell you how it affects you in a fact-based, approachable way. We rely on your financial support to keep making that possible.
Your donation today powers the independent journalism that you rely on. For just $5/month, you can help sustain Marketplace so we can keep reporting on the things that matter to you.