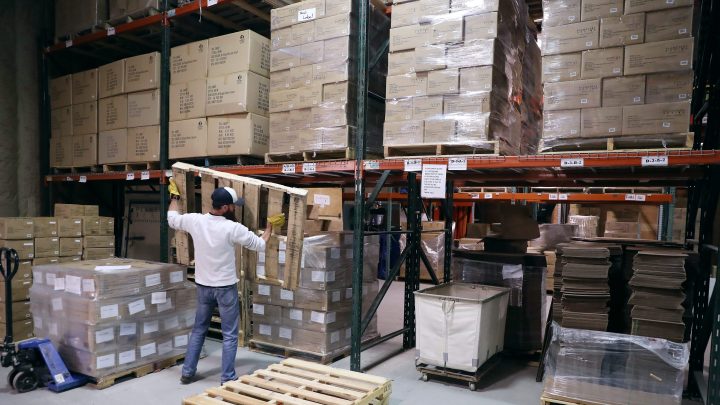
Commercial warehouse use expands at fast pace
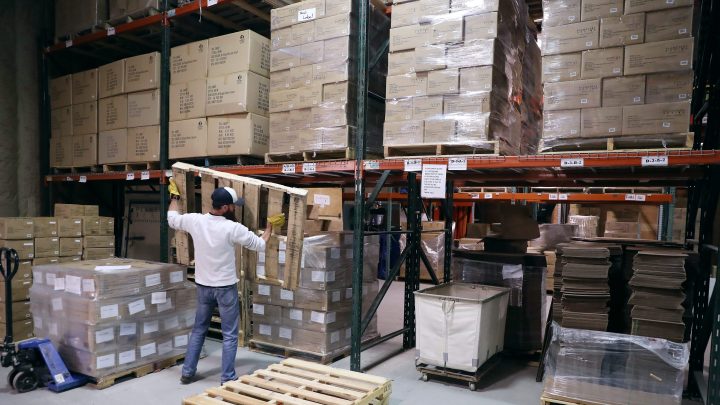
We got a read on the state of the transportation and warehousing industry Tuesday by way of the Logistics Managers’ Index. It found that overall, the logistics sector expanded in September for the second month in a row. A big reason is that companies stocked away more goods in warehouses.
The report found that warehousing “utilization” rose at the fastest pace in six months. So, we checked in with a few businesses that have been stashing away more goods.
Over the last few years, figuring how much product to store in a warehouse has been like watching a wild pendulum.
“We had no goods, then we had too much goods, then it swung back to emptying your warehouse out and putting everything on sale,” said Pat Whelan, who handles imports at Sahadi Fine Foods, a grocery store in Brooklyn, New York.
He said a few months ago, he was trying to keep his warehouses lean. But now, he’s filling them up because he’s got a busy few months ahead. “Christmas, Thanksgiving, they’re food holidays,” Whelan explained.
Thing is, Whelan said he isn’t overordering, like he did early in the pandemic, when supply chains were really congested.
“It costs you a lot more to carry inventory today than it did this time last year, and a lot more than it did two years ago, but you still have to have something,” Whelan said.
The price of warehousing has been rising in part because a lot of new warehouses are opening up in metro areas. And those are more expensive to build in, said Zac Rogers at Colorado State University, who puts together the Logistics Managers’ Index.
Rogers said larger companies can afford to pay those higher warehousing costs. But smaller retailers might be more hesitant because they’ve learned that inventory might not sell.
“The small companies got so hurt last year by having too much inventory on hand that they’re sort of, I think, scarred by it and are terrified to build inventories up too high,” Rogers said.
That said, some retailers are also terrified of not having enough product on hand.
“I think after the shortages during the pandemic, I’ve just tried to make sure I’m not in a position where I’m running low or running out of something,” said Cathrine Reynolds, who manages imports for Palmetto Tile Distributors in South Carolina. She’s been keeping her warehouses full of tile to meet demand because a lot of homeowners are deciding to go ahead with renovations.
“We have a lot of ongoing projects that are just starting to hit. They’ve been in the planning stages for a year or so,” Reynolds said.
And, since Reynolds imports most of her tile from Europe, she wants to ensure she’s protected in case her supply chains become congested again.
There’s a lot happening in the world. Through it all, Marketplace is here for you.
You rely on Marketplace to break down the world’s events and tell you how it affects you in a fact-based, approachable way. We rely on your financial support to keep making that possible.
Your donation today powers the independent journalism that you rely on. For just $5/month, you can help sustain Marketplace so we can keep reporting on the things that matter to you.